Guide To Buy Bulk Pop Rivets
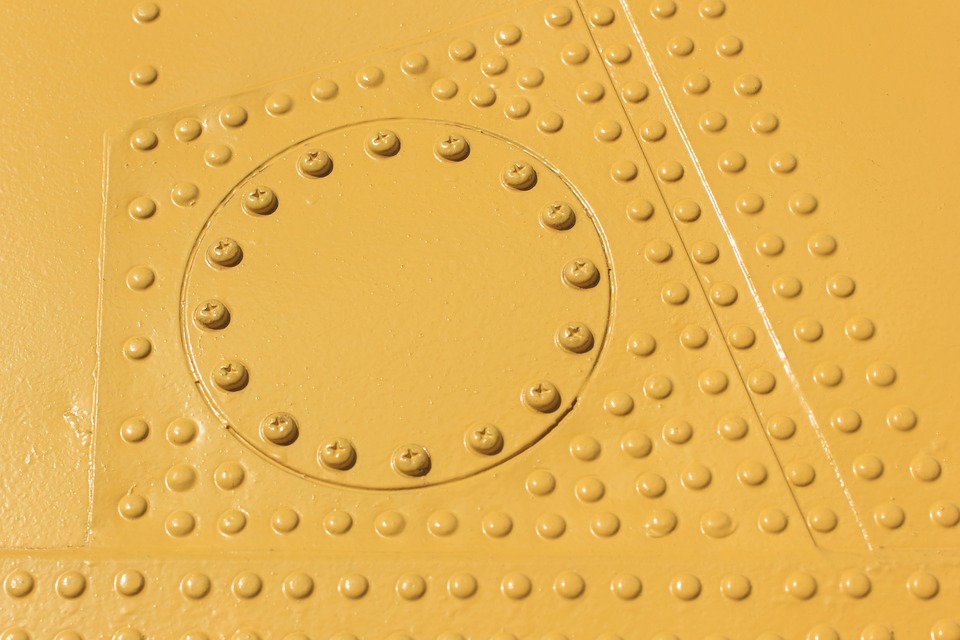
Pop rivets provide a number of key benefits, including easing line-side product control and reducing inventory. They can used in a broad array of applications that have relatively low load bearing requirements. Some of the rivets available on the market are well suited to applications that require tight sealing of water or pressure. Units that are designed with high pull-up capability have the capacity to counteract air gaps, which may be present prior to assembly. On installation, the rivet’s tail is bucked or upset, thus allowing the unit to expand almost twice the original shaft diameter. As a result, it becomes easier to hold the rivet in place. The pounding action creates a new head on one end as the tail is smashed flatter. In the end, the rivet’s shape forms a dumbbell appearance. Technically, the bucked tail is referred to as the shop head or buck-tail while the original head is called the factory head. Each unit can support tension loads thanks to the presence of a head on both ends. However, a rivet is better suited to applications that entail shear loads whereas bolts and screws are ideal for tension applications. Some of the fastenings that use the same principle as the rivet include clinch bolts and copper nails, which work in traditional wooden boat construction. Rivets come in a wide variety of types that are designed to meet different technical requirements, including strength, accessibility and cost factors. Customers who buy bulk pop rivets (also known blind rivets) can apply them in different applications. They are supplied with a non-locking mandrel that is inserted in the rivet’s center. However, the units are unsuitable for critical structural joints since they have the capacity to fall out owing to a variety of reasons, including vibration. The ideal applications provide access from one side. In the early days, people only used solid rivets that require access from two sides of the assembly. On the other hand, structural pop rivets have the ability to handle tensile and shear loads. The unit’s body is made of sheet, tube or wire. Tube is widely used in applications requiring longer lengths while wire is the popular and sheet is the weakest option. Some of the specialty blind rivets available on the market include structural rivets and trifold rivets. Structural variants can be locked internally or externally depending on specific requirements. They are designed to work in applications requiring vibration resistance and waterproof characteristics. Many companies use structural rivets in the manufacture of truck bodies. Trifold rivets, on the other hand, can split into three different legs and are generally used in soft plastics.
Guide To Sheet Metal Fabrication Perth
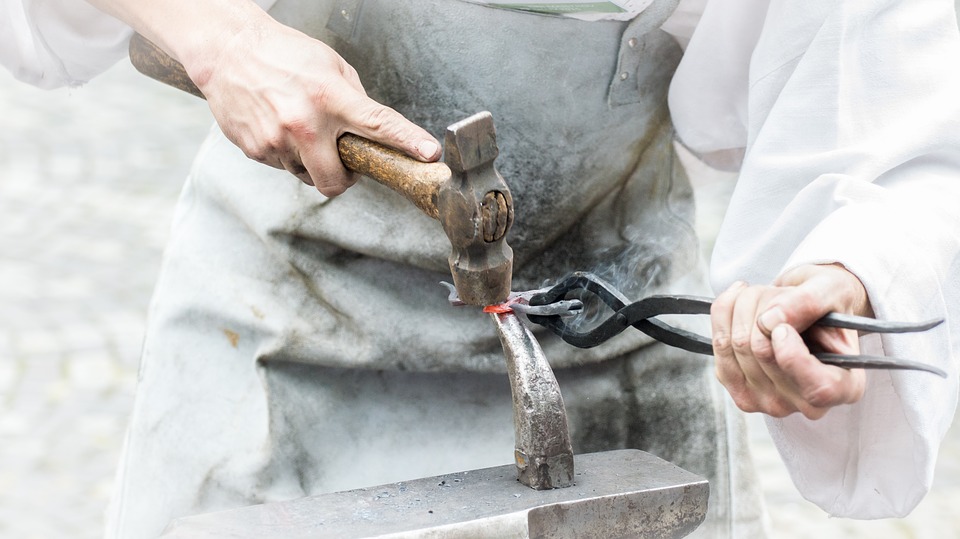
Manufacturability is a key factor that determines design considerations when it comes to sheet metal fabrication Perth. Failure to consider this key aspect can translate to spending a significant amount of time redesigning enclosures and assemblies. The major reason for lack of manufacturability is usually the gap between design elements for sheet-metal parts and the actual fabrication on the shop floor. Lack of in-depth knowledge about fabrication tools can easily compromise the engineer’s ability to develop an accurate design. This may lead to the design of models based on the so-called ‘ideal world.’ In that world, engineers do not have to worry about fabrication imperfections because there are none. This means tolerances and allowances would be always precise. There are no additional considerations, such as real-world material or shop floor behaviour. However, engineers need to formulate designs that take into account factors like collars near hole, spaces between drilled holes and chamfers at the edges. In the real world, some features need alterations to accommodate a variety of key factors. When ignored, this gap can prove costly because it can cause delays and material wastage. The overflowing engineering change orders (ECOs) and redesigning creates a vicious cycle and unwanted inefficiencies, which can be prove difficult to rectify. Closing the gap is an unavoidable requirement in a bid to eliminate sheet metal fabrication errors and costly revisions. A Design for Manufacturability (DFM) strategy makes it easier to achieve this objective. The strategy is aimed at ensuring that engineers do not lose track of manufacturability factors when working on sheet-metal designs. This plays a key role in minimizing or eliminating the possibility of errors by merging the ideal and real world. A DFM strategy helps simplify designs and brings down the number of parts counts. It recommends the standardisation of parts with the aim to use them multiple times in various applications. Design for Manufacturability (DFM) enables engineers to identify designs that are easier to manufacture by providing technical insights during this vital process. Some of the critical aspects of efficient designing include specifying the location, size and alignment of holes. Experts recommend specifying hole diameters that are relatively larger than the sheet metal’s thickness. This is aimed at preventing longer burnish in holes, higher punch loading, slug-pulling when removing the punch and excessive burr. Slug-pulling has been shown to adversely affect the life of the metal sheet and punch. Additionally, it is important to consider spacing between holes to ensure strength of the metal. This also helps prevent the deformation of holes during the bending or forming stages.